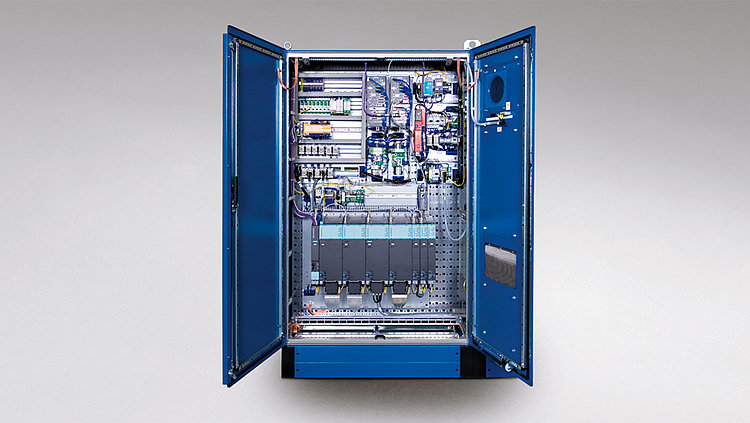
If one of your machines suddenly stops working, you need to react quickly in order to avoid disruption to production and minimise costs. But finding the source of the problem can often be time-consuming, as you have to check every single component. This is where the LQ Group's function-tested modules really pay dividends. They are quick and easy to change so that your operations continue to run smoothly. With their modular control cabinet, LQ's mechatronics experts help to keep machine downtime to a minimum.
By combining standard components into functional modules, LQ has reduced the number of different parts in the control cabinet. Unlike traditional control cabinets, each module in the modular control cabinet has its own input, output and software interface.
Time and cost savings throughout the process chain
Functional modules have many benefits, including a significant reduction in machine downtime. This means that customers can avoid the huge costs involved when machinery is inactive for long periods. LQ modules can be quickly and easily replaced thanks to their separable connectors – a system that really pays dividends. The functional modules can also be installed on-site using the plug & play principle as they are all one hundred percent function-tested and prefabricated. Simply mount the module and connect the relevant interfaces using the pre-assembled connectors – and you’re all set.
"When customers choose one of our modular control cabinets, they benefit from time and cost savings throughout the process chain. This includes savings of up to 30 percent on engineering costs, and the number of different parts and associated expenditure is reduced by up to 50 percent", explains José Quero, CEO of the LQ Group.